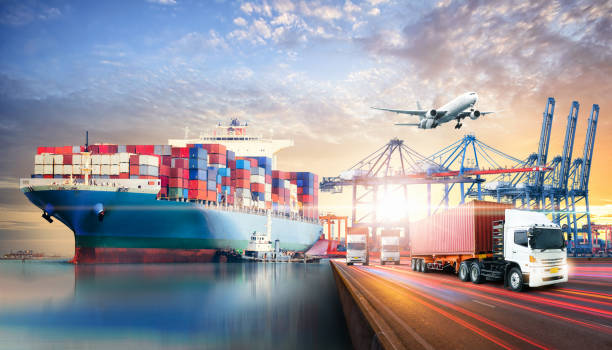
Benefits of Outsourcing Logistics Services | Advantages of 3PL Services | Image Source: istockphoto.com
What is logistics outsourcing?
Utilizing one or more logistics service providers to handle all of your logistics needs, from inventory management through order preparation and delivery, is known as outsourcing logistics.
This directly and broadly translates to the organization having more warehouses and fewer personnel, which a fortiori means that your transport and logistics plan will be optimized.
Outsourcing:
Transferring one or more business operations to a qualified outside service provider is known as outsourcing. Due to this outsourcing, the business is able to concentrate on its core business.
Feel free to contact us for any of your logistical requirements.
How to effectively outsource your logistics?
Should you or shouldn’t you outsource your logistics work? Create a road map before responding to this occasionally difficult inquiry. Because it’s better to outsource effectively if you’re considering doing so!
Define the goals and circumstances of any possible outsourcing to help you select the best choice for your company. The following is a list of crucial considerations:
- Compare the costs of internalizing versus outsourcing logistics: the constant and accounting costs as well as the less quantifiable costs, such as what you might gain or lose in terms of job quality, for instance;
- Take into account the price of closing your warehouse and the cost of your business’s transitional period.
- Do not be afraid to compare estimates from other service providers and benchmark them;
- In order for your outsourcing to be successful, you must build a genuine, long-lasting relationship of trust with your logistics provider. The goal is not just to solve your logistical problems;
- You will also need to collaborate on your company’s internal projects, such as developing financial reports or opening up to global logistics.
The benefits of outsourcing out your logistical operations
There are a lot of advantages to outsourcing. This enables the company to exclusively concentrate on its main business by giving control of its logistics to an expert who will unquestionably be more effective.
Lowering risks for both your employees and your company
By outsourcing your logistics, you may remove a lot of restrictions while lowering possible risk for both your staff and your business:
- It’s no longer your responsibility to maintain or replace equipment used in the supply chain;
- Managing driving hours and adhering to regulations;
- Accounting management;
- The hiring, training, and replacement of workers when necessary;
- Administration of the workforce (payroll, hiring, firing, sick leave, etc.);
- The workforce can be adjusted to your seasonality and activity peaks without incurring additional costs for human resources (recruitment, training, taxes, etc.).
Focus on your business
A business must prioritize its product and commercial development as well as its marketing plan. However, logistical issues frequently take over, necessitating such rapid reaction that businesses have less time to build their core businesses.
The benefits of outsourcing logistics are therefore numerous:
- This enables the business to concentrate on its primary business;
- The organization gains access to a logistics specialist through its external service provider, who can assist it in enhancing specific aspects of its supply chain, such as order processing or deliveries.
- Because of its own partners and negotiated pricing, your service provider may be able to reduce logistical expenses by up to 10% as a result;
- It gives you more flexibility in regard to your sales (connected to the season or your growth) because your service provider can adjust to your increased activity more readily than you can;
- A third-party service provider can help you expand your company globally if it is already well-established in the nation where you intend to expand.
Entrusting your logistics to a logistics services expert could be a smart move if your company lacks agility and logistical issues are affecting your main business. On the other side, you will have better control over internal flows if logistics is at the center of your operation.
The 3 key points to remember:
- Because there are several logistical issues in a company’s daily operations, outsourcing logistics enables you to concentrate on your main business. Utilizing a professional service provider frees you from a substantial number of administrative and technological restrictions.
- But if you have the proper technical and human resources, internal logistics also allow you to better regulate flows and costs.
- This issue needs to be taken into account, be the focus of specifications, and be the topic of an exact comparison of the costs associated with outsourcing vs insourcing.